TECHNOLOGY INNOVATION: 3D printing houses for remote communities?
Is a 3D printed house an option for remote aboriginal houses?
Healthabitat continues to be interested in 3d printing technology. Recently, HH went to visit an almost complete 3D printed house in the southern suburbs of Sydney.
A 3D printed house has the potential to reduce build times drastically, cut out material wastage and use local materials to complete the build, all providing a house that is quicker, cheaper, and more accurate than a traditional build. The idea of cheap, quick, and durable housing for remote communities has been part of the discussion around Aboriginal housing for as long as living memory serves. Healthabitat has spent considerable effort debunking claims of this in the past despite what is promised and has championed cyclical maintenance as the best way to have functional, durable, and affordable housing. Despite this, Healthabitat is always open to new ideas, so let’s explore what the latest company offering 3D housing, Contour 3D, has to offer.
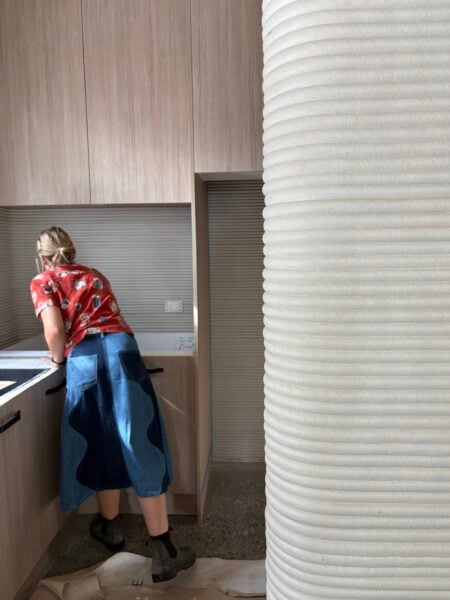
Healthabitat and SA Housing Representatives visited the Sydney home
How does it work?
- In a similar way to a plastic 3-D printer, it builds up a wall from layers of a special concrete mix (cement, sand, additives and water) that gets pumped through a nozzle. The path this nozzle follows is pre-designed and can be made to curve, zig,-zag, etc.
Pros
- Quick to build once the machine is set up and has access to its own batching plant. 16-day print time for 140 tonnes of material (aka single-storey walls for a duplex)
- Concrete allows fixing points for hardware almost anywhere. Great if retrofitting housing for accessibility
- Adjusts print speed to account for temperature, lap time, wind speed and humidity
- 56 MPA (concrete strength) means walls are (virtually) waterproof
- Offers a range of finishes, including a smooth finish
- The quality of water (i.e. hard water, like what is found in many remote communities) doesn’t seem to affect print quality
- The frame and machinery fits on one semi-trailer. and is able to be set up in one day
- Potentially could use 80% local material (once the technology progresses)
- Offers potential for wider than average concrete cavity, meaning a better insulated wall is possible.
Questions and Queries (see more questions and concerns from our last visit in Melbourne December 2022)
- Window and door details not yet well resolved or small tolerances. Limits air-tightness, building energy efficiency and vermin proofing. Contour 3D state this has been resolved with the new gernation of printers.
- The insulation currently used is polystyrene blocks; these are blown into the 200mm wide wall cavity but are hard to ensure have reached all spaces, limiting the effectiveness of the insulation. From inspections onsite Contour 3D and the manufacturer believe good coverage is achieved.
- Plumbing has to be face-mounted to internal walls for bathrooms and rendered over. Perhaps this could be incorporated into the print process to allow less post-print trade work? Contour 3D can leave a cavity as part of the print process to allow for recessed plumbing.
- Not a full building system yet, but rather just 3-D wall system. Currently the 3-D printed wall system has to be accompanied by traditional trade technologies around it. Contour 3D are working to provide a full building system.
- Building using local earth materials, could this make it more of a viable technology for remote and regional communities?
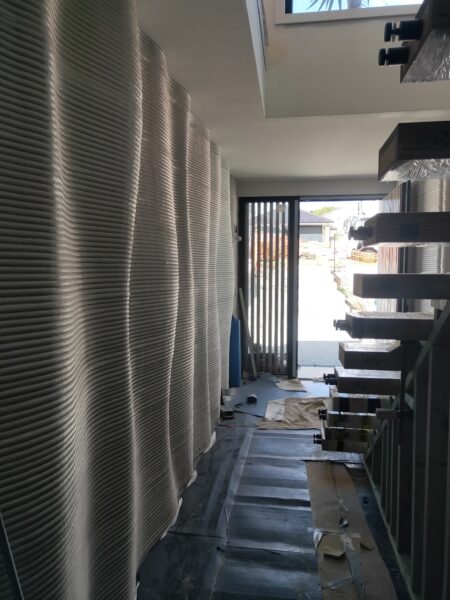
Photo of internal hallway in Duplex – the possibilities of a wall shape
HH is always interested in new technologies and people pushing boundaries to find better solutions. We continue to watch on this technology diligently.